Executive Summary
Much has been written about the global pandemic, which has taken a toll on the entire world. New guidelines and preventive measures are appearing nearly every single day. The most severe impact of this pandemic has been felt by the business world; there is immense pressure on firms to stay two steps ahead while trying to reduce the pressure on margins, and finding ways to keep costs down.
But there is the proverbial silver lining. Opportunities come at times like these, and for firms that are part of core industry verticals, such as construction and manufacturing, it offers the best chance to change the status quo to a large extent, if not completely. Using the twin pillars of digital transformation, and collaboration, these companies can unlock process efficiency, be leaner, and get back on track. It is not easy, but it is certainly doable.
Introduction
Construction firms have a set of routine processes, which they have unfailingly adhered to, for decades. Through such rigid processes, for critical business functions, such as Procurement, Contracts and Subcontracting, Plant and Machinery, Inventory, Financial Accounting, and Payroll, they have seen good economic growth over a period of time.
However, there is a catch. The heavily-debated Kondratiev economic cycles come into play. For the first forty to sixty years, give or take a few, the world witnesses high economic growth in almost all business sectors. Then, there is a period of relatively slower, or low, growth. Combine the latter with events such as global economic recessions, falling demand, and the current COVID 19 pandemic, and suddenly these firms realize the constraints posed by their existing business systems and manual processes.
Let us consider Procurement, and Subcontracting, for example. More specifically, we will focus on the material supply chain, as well on invoicing, and the Subcontracting process.
Challenges in the Material Supply Chain
From requisitions to delivery and receipt, the entire cycle lacks collaboration between various teams and has no seamless flow of information.
- Requisition and Purchase Order Delays– There are cases where people get increasingly anxious when trying to requisition materials based on project demand. The Buying team is fighting fires in every direction, and does not have time to scrutinize, carefully, the burgeoning queue of emails, or deal with the insurmountable piles of paper requests. As a result, any clarifications sought from the requesters are not included, causing confusions and misunderstandings. Moreover, the decisions to place purchase orders are delayed, sometimes for weeks or months on end. Even if requisitions are captured in the systems that businesses have, the task of proactively assigning them to the Buying team, is as cumbersome as raising the requisition itself. By the time the request is worked upon, and the purchase orders are prepared, crucial time is lost.
- Delays in entering Goods Receipt Notes – When the requested materials are finally delivered, a Goods Receipt Note is recorded; however, existing systems do not make this easy for users, owing to various factors. This exacerbates things even more. The entire process needs to be restarted, and more time is, therefore, lost.
- Impact on Invoicing – Invoicing, in such situations, becomes extremely difficult for the Accounts Payable team. While paper-based AP and AR documents have their own set of challenges, electronic documents also tend to be confusing, with regards to the information that must be entered in the invoice. Not only are the delays inordinate, but also these documents are prone to errors. When businesses process invoices for the equipment (referred to as Plant in the industry) they hire externally, they need to factor in a lot of variables, such as hire charges, idle time for the Plant, or the duration for which the Plant was deployed on the project, either fully or partially, to name a few. Many documents need to be referenced, plenty of conversations take place between teams, physical copies of Plant registers are opened and looked into.. the list is endless. Though these are eventually sorted out, valuable time has been lost into getting the required information. Also, matching invoices, and ensuring that the suppliers are paid on time, become bottlenecks due to a complete lack of comprehensive collaboration, as well as the absence of simplified documents for these vital business functions.
The challenges in Subcontracting
The current pandemic has, once again, brought into prominence the need for collaborating with the external supply chain, as well as agility and adaptability to both internal and external factors. While the need for agility may refer to the execution of projects, collaboration becomes even more crucial in the context of subcontractors, whose specialized skills are brought onboard, in order to get the most critical aspects of the project completed without errors, and on time.
- The Valuation Challenge – In the present scenario, quantity surveyors inspect the work done by a subcontractor, certify the units of work completed, and assign value to these units. Because work completion valuation is a vital part of the Subcontracting to Payables cycle, it is prudent to be thorough. But, the present mechanism employed by the quantity surveyor is tedious and involves discussions/debates at various levels, just to certify a single activity. As a result, project budgets, schedules, and costs, are susceptible to overruns. Coupled with the tasks of managing claims and disputes, along with the inherent complexities of the valuation document created in the firm’s current software system, the situation becomes much more complicated.
- Paper Trail – In the case of subcontractors, if they use paper-based records to keep track of the work that they have done, it becomes problematic for the contracting company, or client, to go through all those records. This problem intensifies while trying to validate subcontractor tasks, so that payments can be authorised.
- Compliance Tracking – Businesses that maintain paper based lists of subcontractors or suppliers, often find it difficult to validate their credentials, resulting in delayed start of projects.
The Power of Xpedeon – Streamlining Procurement and Subcontracting
Algorithms ’purpose-built ERP system, Xpedeon, drives digital transformation, in the construction and allied verticals, through an innovative approach. Not only does Xpedeon address mission-critical problem areas, such as tracking budget & project schedule overruns and deviations, but also provides detailed insights into aspects such as monitoring inventory position, ensuring that Buy or Make decisions are taken quickly, making live data available for analysis & rapid decision making, and so on.
- “Digital” Procurement – Xpedeon digitizes the Procurement function through easy-to-use forms and screens, from Requisitions to Purchase Orders. All you have to do is enter the basic information, and your requisition is ready to go. With a pre-defined list of approved suppliers, subcontractors and other external parties, the Purchase Enquiry process, though optional, becomes much more simple. Using the Supply Chain Portal, which links up with the core system, allows these external parties to respond to enquiries with their quotes and detailed information, on the click of a button. Xpedeon also contains the Procurement Workbench feature, with which the Procurement professionals can easily be allocated requisitions, and quickly convert them into Enquiries or Orders, depending on the requirements.
- Going Mobile – With the Xpedeon Mobile App, you can execute the entire Procure to Pay cycle, on the go. Requisitions, Approvals, Nominations, Purchase Orders, Recommendations – every aspect of this cycle is covered quickly, and effectively. With such powerful capabilities, construction firms can enter the so-called New Normal, with absolute confidence that their processes are in safe hands. Key functionalities such as Remote GRNs, for example, enhance the ability of Xpedeon to provide a complete solution.
- Effective Subcontracting – The use of electronic forms of documents, such as Applications for Payment, Payment Certificates, Progress Measure, and so on, simplifies the Subcontracting process as a whole. The format of these documents is easy to understand, so data entry becomes much more simple. For example, the Application for Payment allows subcontractors to send their “itemized application for services rendered”, thus reducing the involvement of quantity surveyors. In addition, the system also ensures that subcontractors enter completed units of work, which do not exceed the contracted units of work. Further, the Supply Chain Portal provides an additional thrust by giving potential new subcontractors a place to enter their details and bids.
- Robust Reporting– Reporting, one of the multiple “mission critical” requirements of any firm, is easily handled by Xpedeon’s powerful framework, through various reporting tools. OLAP cubes, visualization, pre-defined templates which can be tailored to customer needs, “seeded”(pre-built) reports – all of these combine together to provide an enriching reporting experience, and enhance decision making, as well as collaboration.
In conclusion, Digital transformation, in the Xpedeon way, is the answer to your pressing needs.
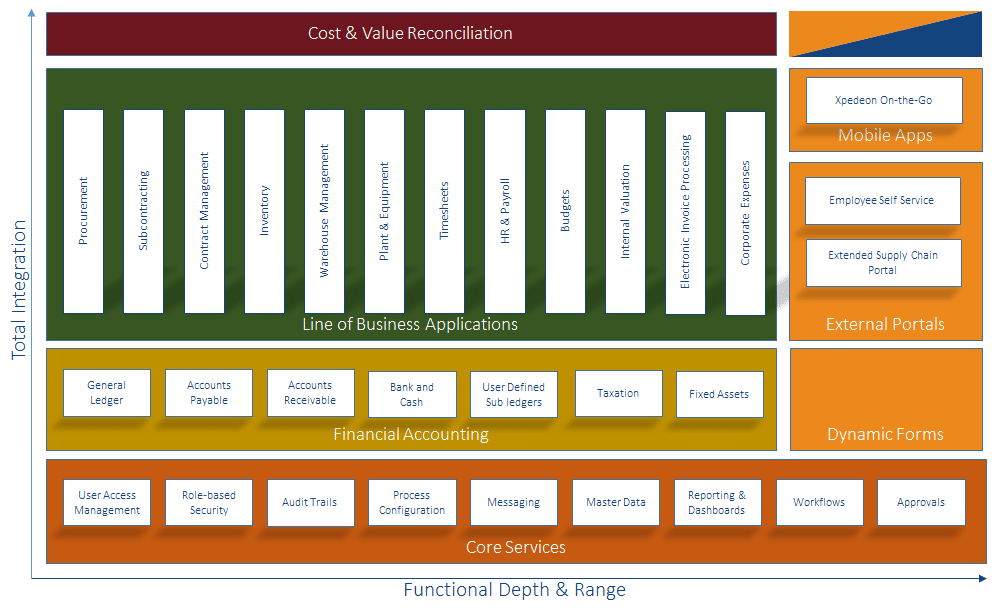
Share this Post